Introduction: Why Barcodes Are the Real MVP of Inventory Management System?
Picture this: You’re trying to run a store, but you have no clue what’s on your shelves or what’s gathering dust in the back. Total nightmare, right? That’s what it’s like if you don’t have a solid inventory management system. Enter barcode labels—the unsung heroes that bring order to the chaos. They make tracking and managing your stock as easy as pie. In this guide, I’m going to show you how to integrate barcode labels into your inventory management system, saving you time, reducing headaches, and making you wonder why you didn’t do this sooner.
Understanding Barcode Technology: What You Need to Know Without the Jargon
What Are Barcode Labels, and Why Should You Care?
Think of barcode labels as cheat codes for your inventory. They’re those little black-and-white stripes or squares you see on products everywhere. Scan them, and voilà—you instantly know everything about that item. It’s like having a magical list that keeps track of everything so you don’t have to.
Types of Barcodes
1D Barcodes :
These are the traditional linear barcodes consisting of a series of lines and spaces. They’re simple, reliable, and perfect for basic tracking
2D Barcodes:
Now, these are the fancy ones, like QR codes. They can hold way more information than 1D barcodes and are great when you need to pack a lot of data into a tiny space.
Benefits of Using Barcodes in Inventory Management System
- Accuracy: Manual data entry is a breeding ground for mistakes. Barcodes cut out the middleman and give you spot-on accuracy with every scan.
- Efficiency: What used to take hours (and a ton of patience) now takes minutes. Scanning barcodes is like putting your inventory management on fast-forward.
- Inventory Control: With barcodes, you’re always in the loop. Real-time updates mean you know exactly what’s in stock and what’s running low.
Prerequisites for Integrating Barcode Labels
Getting Ready: The Stuff You Need Before Diving In
Hardware :
- Barcode Scanners: These are your new best buddies. They read the barcodes and instantly update your inventory—no typing required.
- Barcode Printers: A regular office printer won’t cut it. You need a specialized barcode printer to ensure your labels are crisp and easy to scan.
Software:
- Inventory Management Software: Ensure your inventory management software is compatible with barcode technology. You might need a plugin or an update, but it’s a small tweak that’ll make a huge difference.
Staff Training :
- Proper training is key to making sure everyone’s on board and things run smoothly right out of the gate.
Step-by-Step Integration : How to Get Those Barcodes Up and Running
Step 1: Take a Good, Hard Look at Your Current Setup
Evaluate your existing inventory management system to determine its compatibility with barcode technology. Identify areas that need improvement and plan for the integration process.
Step 2: Choose the Right Barcode Labels
Not all barcode labels are created equal. Think about what will work best for your inventory. Do you need something that can handle wear and tear? Is readability a top priority? If you’re not sure, get assistance with a barcode label manufacturer/supplier who can help you figure out the best options.
Step 3: Setting up Printers and Scanners
Time to get your barcode printers and scanners up and running. Install and configure barcode printers and scanners. Ensure they are properly connected to your inventory management software.
Step 4: Update Your Software
Make sure your inventory software is barcode-ready. Update your inventory management software to support barcode scanning and printing. This may involve installing plugins or additional modules.
Creating Barcode Labels: How to Get It Right the First Time
Designing Your Barcode Labels
When designing barcode labels, you want them to be clear, easy to read, and packed with all the necessary information. Use quality barcode printing software to create accurate and high-quality labels.
Best Practices for Label Creation
Durability Matters: Use durable materials for labels to withstand environmental conditions. Consider using synthetic labels that are designed to withstand harsh conditions and frequent handling. These labels are waterproof, resistant to moisture, and can endure exposure to liquids and chemicals. For the best results, consult with top specialty label manufacturers to find the perfect solution for your needs.
Contrast Is Key: Ensure barcodes are printed with high contrast for easy scanning.
Implementing Barcodes in Inventory Management System:
Labelling Your Existing Inventory
Start by labelling everything you’ve already got in stock. Although, it’s a time-consuming process but it is very essential for a smooth transition.
Adding Barcodes to New Inventory
Make sure every new item gets a barcode as soon as it comes in. That way, it’s ready to be tracked from the get-go.
Setting Up Scanning Procedures
Create a standard process for scanning items into your system. Consistency is key—it’s like developing a good habit that keeps your inventory in check.
Testing Your System: Making Sure It’s Ready for Prime Time
Before you go all-in, run some tests with a few items to make sure everything works like it’s supposed to. Better to catch any hiccups now than deal with them later.
Troubleshooting Common Issues
Identify common issues such as unreadable barcodes or scanner malfunctions. Troubleshoot these problems promptly to maintain system reliability.
Regular Audits: Keeping Everything Shipshape
Regularly audit the system to ensure data accuracy. Implement checks and balances to maintain the reliability of your inventory management system.
Training Your Team: The Last (but Crucial) Step
Barcode technology is only as good as the people using it. Make sure your team knows the ins and outs of the new system. A little training goes a long way in preventing headaches down the road.
Keep the Support Going
Don’t just train your team once and call it a day. Keep offering support and updates to make sure everyone stays sharp and your inventory stays accurate.
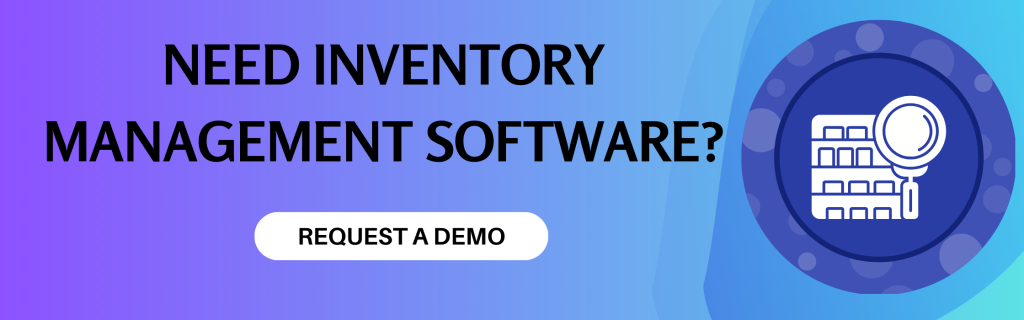
Case Studies
Real-Life Wins: How Big Names Are Killing It with Barcodes
Amazon:
Amazon uses barcodes to track everything, from the warehouse to your doorstep. This keeps errors low and efficiency high, making their service reliable and fast.
Walmart:
Walmart’s barcode system lets them track inventory in real-time, ensuring shelves are always stocked and customers find what they need—no more “out of stock” disappointments.
Zara:
Zara uses barcodes to keep up with fast-changing fashion trends. They track items from production to store shelves, allowing them to respond quickly to customer demand.
Integrating barcode labels into your inventory system is a game-changer. You’ll see improved accuracy, speed, and control over your stock. Plus, with real-time tracking, you’ll always know what you have on hand and where it’s going. It’s like having a superpower for your inventory management—one that you won’t want to live without.
Ready to dive in? Start integrating barcode labels today and watch your inventory management transform from a chore into a streamlined, efficient process. If you need assistance, don’t hesitate to reach out to Codentrix Technologies. We specialize in helping small, medium, and large enterprises with everything from barcode printers and labels to complete inventory management software integration.